Rotational Moulding
Rotational moulding is a production process that is particularly suitable for large, hollow products. We can produce parts with uniform wall thickness and complex shapes, at a relatively low production cost. The production method means that you get a homogeneous material with low tension and no welding seams.
Get in touch
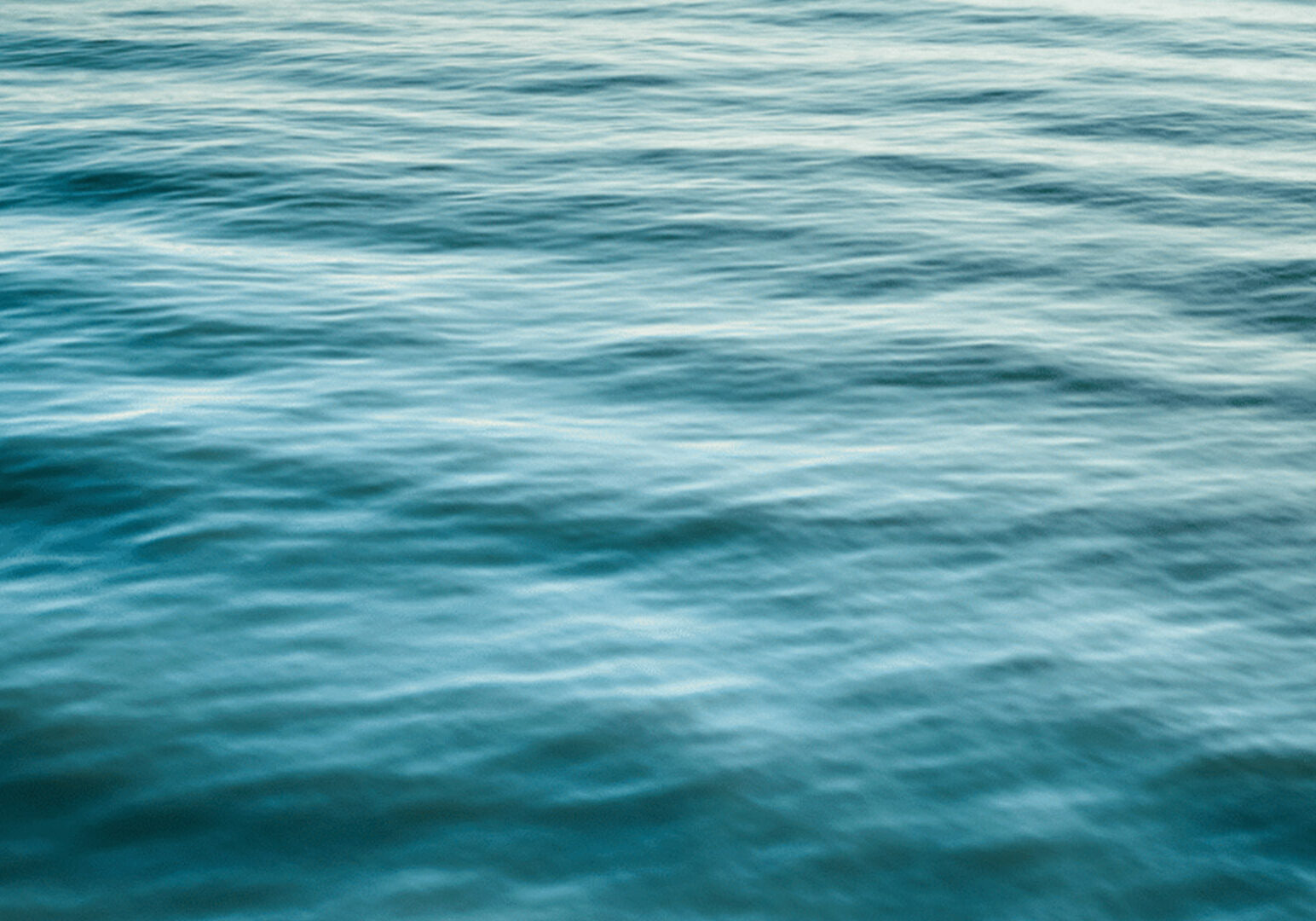
Rotational moulding
Moulds are first filled with small plastic pellets. The mould is then heated and rotated, using centrifugal force to coat the inner walls of the moulds with plastic. No additional pressure is required during the casting.
Additional processes can be added; for example filling with polyurethane foam or epoxy filler. Rotational moulding offers the opportunity to manufacture stress-free parts with uniform wall thickness and complex shapes at a relatively low production cost.
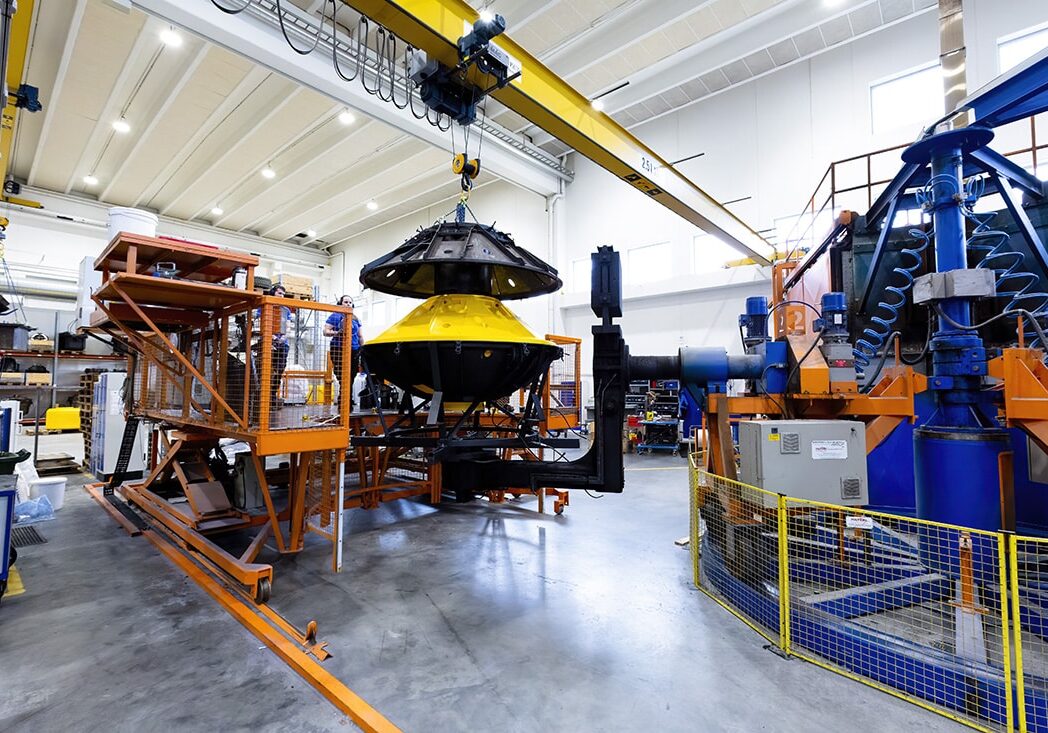
Materials
Medium and High Density Polyethylene (MDPE, HDPE) are the materials of choice for roto-moulding at Ovun. These materials are fantastically durable and versatile.
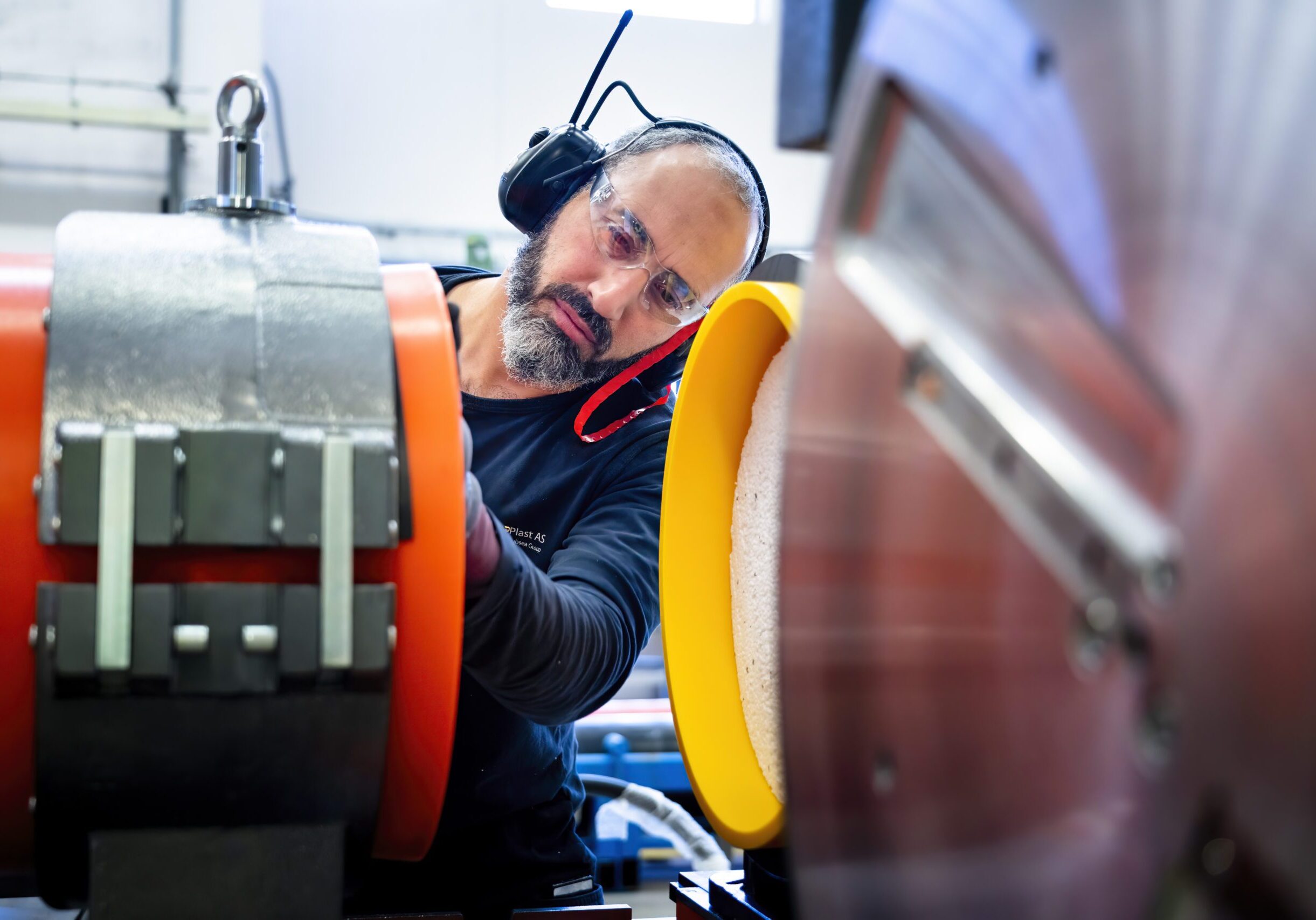
Experience
We have a long history of development, innovative thinking and design in its various segments. Plastic products can be used in combination with components of steel and aluminium as well as integrated electronics systems.
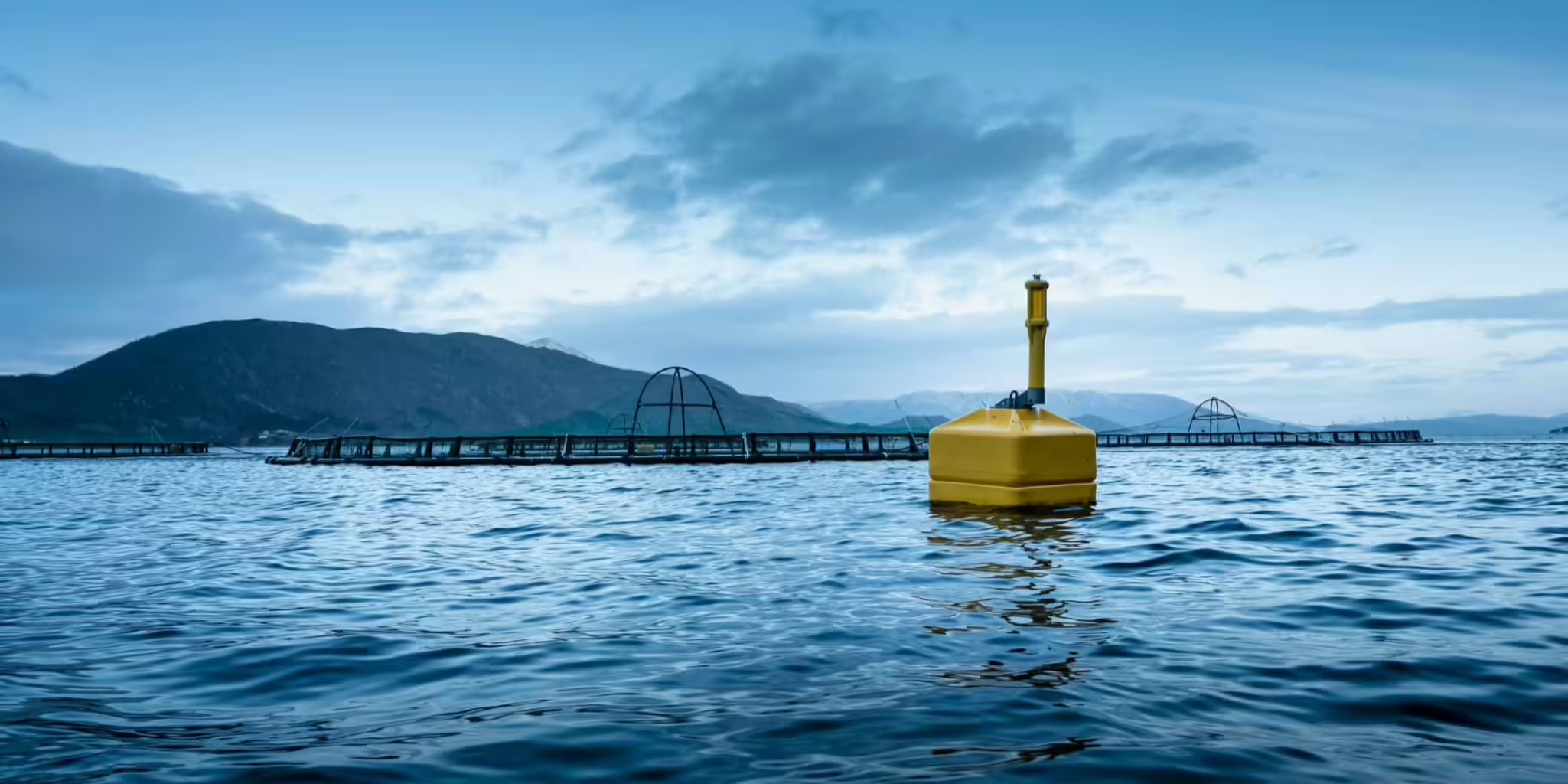
Advantages
-
Low internal stresses
-
Rotational moulding
-
Relatively low tooling costs
-
No welding seams
-
Large products at low cost
-
Design freedom - realise your dream